Why CSD bottle design different between water bottle
The first plastic bottle appeared on the market in an attempt to replace glass for CSD application is in 1978 by Coca-Cola company. Before that, carbonated soft drinks are packaged in a glass container, which poses two major disadvantages: breakage when dropped and being too heavy for transportation. Therefore plastic counterparts were looked into, and PET was the chosen material, and for a good reason: transparency, lightweight, and shatter resistant.
The first PET bottle for CSD application comes in two parts, the PET bottle with a round base and a base which glued at the bottom for up-right standing. However, this solution requires two separate manufacturing processes and the base cup is made of different materials from the body, which poses a recycling issue. It is until the early 90’s that the three-piece mold technology was introduced. The integrated base PET bottle became economically feasible and revolutionized rigid packaging for the entire beverage industry.
(Extended reading: How a beverage vendor selects the suitable PET blow molding machine)
PET Bottle Stretch Ratio
PET is the ideal replacement material for glass due to its physical property after being stretched, since the random molecular structure would be in a more aligned state after being stretched at a specific ratio (2.5-3 times for example). At this ratio, PET underwent a plastic deformation, and when processed under dual-axis forming procedures such as the stretch blow molding process, the material is oriented in two directions making it stronger while improving the CO2 retention.
CSD Bottles Definition
What makes a CSD bottle different from a water bottle is its’ ability to withstand internal pressure before bursting. For CSD application, the bottle needs to be able to withhold up to 10 bar of pressure before failure (some stated average of 8.6 bar). This is achieved by the petaloid form of the base, since this form would greatly increase the surface area at the bottom, meaning the base gets stretched out more and is able to sustain higher pressure.
There are several factors are known in the industry which might affect the bottle performance:
- PET molecular orientation.
- degree of crystallinity at the base.
- PET IV value.
- Stretch ratio.
- Stretch speed.
- Stretching temperature.
The more orientated the material at the base means the higher degree of crystallization.
A higher IV value is also desired for the process if preform lost too much IV value due to the non-optimum injection processing parameter, and the dropped IV value as result. It would affect the bottle's performance. A higher stretch ratio and speed will also increase the orientation. Higher stretch temperature decreases the molecular orientation when stretching. All these play an important role in the ability of the bottle to withhold pressure and must be taken into consideration when processing them.
Soft Drink PET Bottle Making Machine Manufacturers
CHUMPOWER MACHINERY CORP. has more than twenty years of experience in the PET stretch blow molding machine domain. CHUMPOWER has a rich experience in manufacturing, professional pre-sales inquiry services, and complete after-sales services. We export our products to over 103 countries, and the brand “CHUMPOWER” is dearly trusted and highly evaluated by our customers. We can provide you with more than just the finest PET stretch blow molding machines, preforms, molds design, and the planning of a whole production line, but also the smart blow molding machine system, we are the best choice.
(Extend Reading: BottleViewer, everything bottle blowing related is right at your hand)
Welcome to Contact Us!
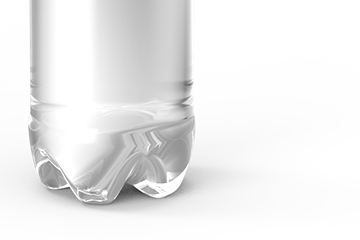